銅鈷礦選礦方法及工藝流程介紹
2021-09-29 來源:鑫海礦裝 (2659次瀏覽)
鈷是一種重要的戰(zhàn)略金屬,由于其良好的物理、化學及其機械性能,被廣泛應用于航空航天、機械工業(yè)、化學工業(yè)、陶瓷工業(yè)以及合金制造等領域。世界上的鈷絕大部分是以副產品形式產自風化型紅土鎳礦、巖漿型硫化銅鎳礦和沉積型砂巖銅礦之中。中非作為世界銅鈷的主要的產地,現階段中非銅鈷礦帶的礦床多為氧化礦,其選礦工藝主要以浮選、磁選、浸出為主。
一、銅鈷礦浮選工藝及流程
浮選是選別銅鈷礦石的主要工藝之一,主要工藝包括銅鈷依次優(yōu)先浮選以及銅鈷混合浮選,然后,再采用其他方法進行分離。
工藝流程:
一先將銅鈷原礦進行磨礦處理,在磨礦過程中添加一定量的調整劑,調整礦漿的pH值至9-10范圍內。磨礦處理后的礦漿中依次加入捕收劑和起泡劑,進行銅鈷混合浮選粗選,并在兩次掃選后得到尾礦。在混合浮選泡沫中加入抑制劑,進行三次精選后得到銅鈷混合精礦,依次加入抑制劑和捕收劑,進行銅鈷分離浮選,并經一次粗選、一次掃選后得到鈷精礦,對銅鈷分離浮選后的泡沫進行兩次精選后得到銅精礦。
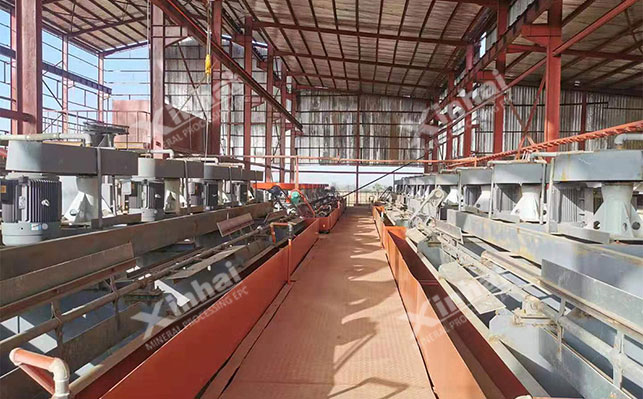
該工藝適應性強,不僅可回收低品位、嵌布復雜的細粒銅、鈷礦物,同時降低了銅、鈷礦物分離難度,顯著提高了銅、鈷精礦的質量與回收率;且操作簡單,可控性強,對礦石適應性也較強。但是受現有技術的限制,采用單一浮選方法很難使銅鈷礦有效分離,因此多余其他工藝聯合使用。
二、銅鈷礦浮選-磁選聯合工藝及流程
中非銅鈷礦帶成分復雜,大部分情況下浮選無法將鈷全部回收。鈷具有弱磁性,可配合磁選工藝對其進行回收。銅鈷礦浮選磁選聯合工藝已經成為提高氧化礦選礦回收率的有效手段。
工藝流程:
先將銅鈷氧化礦浮選尾礦用球磨機磨碎至-0.074mm占70-90%,配成濃度為10-40%的礦漿,用0.8-1.2T背景場強高梯度磁選機進行強磁粗選,得到強磁粗選精礦和強磁粗選尾礦,強磁粗選尾礦為最終磁選尾礦。
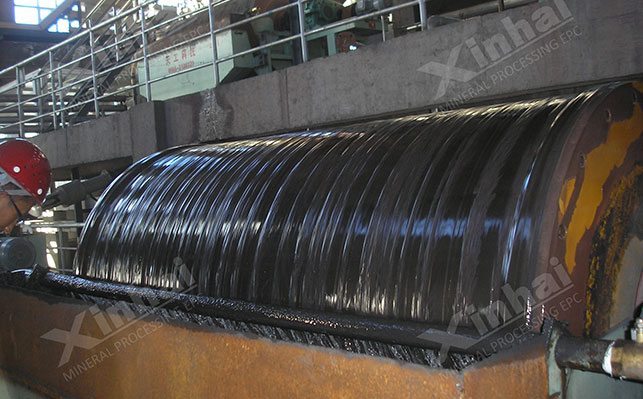
強磁粗選精礦用0.8-1.2T背景場強高梯度磁選機進行強磁精選,得到強磁精選精礦和強磁精選尾礦,強磁精選尾礦為最終磁選中礦;再將強磁精選精礦磨碎-0.037mm占50-80%,配成濃度為10-40%的礦漿,用 0.08-0.15T背景場強高梯度磁選機進行弱磁選,得到弱磁選精礦和弱磁選尾礦,弱磁選精礦為最終磁選精礦,弱磁選尾礦為最終磁選中礦。
該方法適用于含磁性物質較多的氧化礦,能有效提高磁選精礦品位。
三、銅鈷礦浸出工藝及流程
對于復雜氧化銅鈷礦,通常采用浸出等方式處理。氧化礦石普遍風化嚴重,滲透性能不好,不適合全部堆浸。堆浸與攪拌浸出相結合能夠獲得高的銅、鈷金屬回收率。
工藝流程:
先將氧化銅鈷礦原礦破碎磨礦,根據粒級將破碎后的礦石分級。+5mm粒級產品采用堆浸,采用分階段堆浸,先噴淋浸銅,pH 值控制在1.5,噴淋強度為10~15L/m2 . min,浸出時間為60~120天;-5mm粒級產品浸出攪拌浸出,攪拌浸出在常壓下進行,反應溫度為20-80°C,PH值控制在1. 5,浸出液固比為4:1,磨礦細度-200目占60%~90%,浸出時間小于4小時。
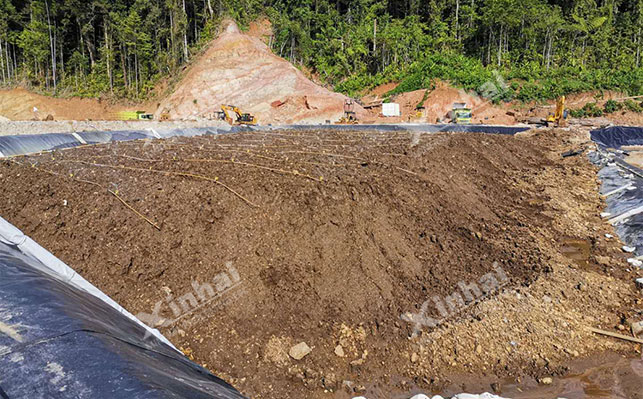
該法減少了試劑消耗,簡化工藝流程,便于實際操作。同時鈷回收率提高了20%左右,較傳統(tǒng)攪拌浸出工藝比節(jié)省建設投資15%左右,較傳統(tǒng)堆浸工藝比銅回收率提高12%左右,有效提高了投資回報率。
以上就是常見的三大銅鈷礦選礦工藝。在實際生產中,建議礦主們做好選礦試驗,根據銅鈷礦石的組成成分及自身的選廠條件、投資成本,咨詢具有專業(yè)選廠資質的廠家,制定科學合理的銅鈷選礦方法,以確保理想的銅鈷選礦指標,保證選廠經濟效益。